Top Rated Food Safe Wood Coating Resin with Fast Thin Film Set and VOC Free Formula
By:Admin
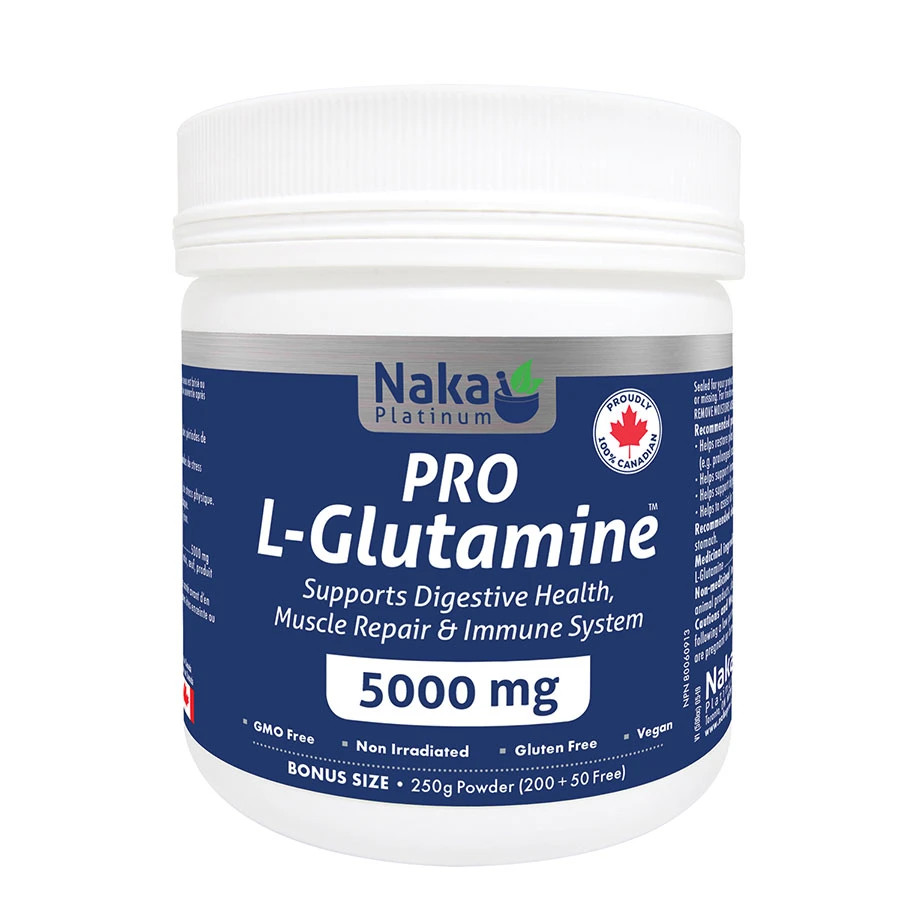
ProMarine Epoxy Coating and Casting Resin is an excellent choice for those who want a product that is both versatile and easy to use. It has a 1 to 1 ratio, which makes measuring and mixing a breeze. Additionally, the fast thin film set of just 6 hours means that you can complete your projects in a shorter amount of time.
The food-safe rating, as well as the ability to withstand heat and other environmental factors, makes it an ideal choice for kitchen and dining room table projects. The coating resin also provides extra protection for outdoor woodwork projects like decks and patio furniture.
What sets ProMarine Epoxy Coating and Casting Resin apart from other wood coating resins is its ability to be used for casting as well. The 7.57 L pack size is perfect for creating intricate molds with Aldax Moulds.
One major highlight of this coating resin is that it is completely free of VOCs, or volatile organic compounds. VOCs can be harmful to the environment and human health, so it is reassuring that ProMarine Epoxy Coating and Casting Resin is an eco-friendly option.
ProMarine Epoxy Coating and Casting Resin is a worthy investment for woodworking enthusiasts who want a high-quality product that offers consistent results. Whether you're a beginner or an experienced woodworker, this product is a must-have in your toolbox.
In conclusion, for those in search of the best wood coating resin of 2020, look no further than ProMarine Epoxy Coating and Casting Resin. Its versatility, food-safe rating, quick-drying time, and eco-friendly properties make it a standout choice. Get your hands on this incredible product today and see the amazing results it can deliver.
Company News & Blog
Understanding Curing Agents: Types and Functions
Curing agents are substances that are used to harden reactive oligomers, ensuring that they do not remain in their liquid or gaseous state. In other words, curing agents help to ensure that reactive oligomers - which are a component of most polymers - are converted into a solid state. There are different types of curing agents that are available, and they are classified into three groups based on their activity.The first group of curing agents are those that have a very low activity level. These curing agents are typically used when the reaction needs to be initiated under very specific conditions, like when a specific temperature needs to be reached before the reaction can begin. The second group of curing agents are those that have a higher activity level. These are typically used when the reaction needs to begin quickly, or when there is a need for a rapid curing process.The third group of curing agents are those that have a very high activity level. These curing agents are typically used when the curing process needs to be accelerated even further, or when the process needs to be completed in a very short amount of time. These types of curing agents are often used in industrial settings, where there is a need for rapid production and curing times.Curing agents can be used to harden a wide range of materials, including polymers, plastics, and resins. They can also be used to create a range of different products, from adhesives and sealants to protective coatings. One of the key benefits of using curing agents is that they help to ensure that the final product is of a high quality, with strong and durable properties.Another key advantage of using curing agents is that they can help to improve the overall production process. By curing materials quickly and efficiently, curing agents can help to reduce production times and costs, while also reducing waste. They can also help to ensure that the production process is consistent and reliable, which is essential in industries where a high level of quality control is required.Overall, curing agents are essential components in a wide range of industrial applications. As technology continues to advance, we can expect to see even more innovative and effective curing agents being developed, helping to make the production of high-quality materials faster, more efficient, and more cost-effective.
DOE Provides Funding for Development of Energy-Saving Automotive Paints and Coatings
PPG Receives DOE Funding For Energy-Saving Automotive CoatingsPPG, one of the world’s leading manufacturers of paints, coatings, and materials has received funding from the U.S. Department of Energy (DOE) to continue its research into energy-efficient coatings for the automotive industry. According to the company, this latest round of funding will allow PPG to further develop its innovative coatings systems and accelerate the adoption of new technologies to help minimize energy consumption and waste.As part of the DOE’s research initiative, PPG will work with various automotive and coating industry stakeholders to determine the best way to reduce the energy required for the traditional painting and coating process. The company will leverage its years of experience in developing and implementing sustainable solutions to address this issue. As part of this, PPG will focus on implementing new, energy-efficient manufacturing processes to reduce energy consumption and greenhouse gas emissions. “At PPG, we have always placed an emphasis on creating sustainable products and processes that help to minimize environmental impacts,” said Tim Knavish, PPG’s senior vice president of automotive coatings. “As part of this new initiative, we plan to collaborate with industry experts and technology leaders to help accelerate the implementation of energy-efficient coatings systems in the automotive industry.”According to PPG, its new coatings technologies are designed to help automakers meet increasingly stringent emissions regulations while also improving the longevity and durability of automotive coatings. Additionally, the company stated that its coatings provide increased scratch resistance, greater color consistency, and improved efficiency compared to traditional coating methods.The DOE funding will enable PPG to further develop its innovative coatings technologies, with the intention of penetrating new markets and addressing the unique needs of the automotive industry. Through this process, the company hopes to support the industry’s efforts to reduce waste, decrease energy consumption, and promote a more sustainable future. Ultimately, PPG hopes to contribute to a cleaner, healthier planet by creating environmentally-friendly products that help to minimize the industry’s carbon footprint.PPG is no stranger to working with the Department of Energy. In 2018, the company received $1.5 million in funding from the DOE to aid in developing new technologies that would reduce the time and energy required to bake automotive coatings. That funding allowed PPG to explore the use of ultra-violet (UV) light to cure coatings into a hard, durable finish, rather than using a traditional baking process. This new process significantly reduces the time and energy needed to complete a coat of paint and could have a tremendous impact on the industry.“We’re excited to continue our partnership with the DOE and explore new technologies that will help the industry transition to more sustainable practices,” said Knavish. “By working together, we believe we can make a significant impact on the future of the automotive industry and the well-being of our planet.”PPG’s commitment to sustainability, innovation, and collaboration has made it a leader in the coatings industry, and the company’s latest funding from the DOE is a testament to the breadth and impact of its research. As the company enters a new phase of development, it remains committed to creating environmentally-friendly coatings systems that will help to support a cleaner, healthier planet.
Industrial Grade Epoxy Floor Coating Kit: 5x Thicker than Paint
article on the benefits of using industrial epoxy floor coatings.Industrial Epoxy Floor Coatings: The Ultimate Solution for Durable and Attractive Industrial FlooringIf you're looking for a flooring solution that offers durability and aesthetics, industrial epoxy floor coatings are the perfect choice. These coatings are widely used in various industries, including manufacturing, warehousing, automotive, pharmaceuticals, and healthcare. They are known for their strength, resistance to wear and tear and the ability to withstand heavy traffic and harsh chemicals.Epoxy coatings are a popular flooring option for industrial settings because of their long-term benefits. These coatings provide a seamless and non-porous surface, making them hygienic and easy to clean. In addition, they are resistant to moisture and chemicals, which helps to prolong the life of the flooring.Here are some benefits of using industrial epoxy floor coatings:Durability and Longevity: Epoxy coatings are renowned for their strength and durability. They are resistant to wear and tear, making them ideal for industrial environments where heavy machinery and equipment are used. Epoxy floors can last up to 10 to 20 years if maintained properly.Easy to Clean and Maintain: Industrial epoxy floor coatings are easy to clean and maintain. They are seamless, which means there are no cracks or seams where dirt and debris can accumulate. All you need is a mop, bucket, and some mild detergent to keep the floors clean and hygienic.Resistant to Chemicals: Epoxy coatings are resistant to a wide range of chemicals. They can withstand exposure to oils, grease, acids, and alkalis, making them ideal for industries such as manufacturing, automotive, and pharmaceuticals.Attractive and Aesthetically Pleasing: Epoxy coatings are available in a range of colors and patterns, allowing you to create a customized and attractive floor. You can choose a color that matches your brand or a pattern that complements the design of your facility.Improved Safety: Epoxy coatings can be slip-resistant, which improves safety in the workplace. You can choose a coating that has a non-slip surface to reduce the risk of slips and falls.Easy Installation: Installing epoxy coatings is a quick and easy process. The coatings can be applied directly over the existing concrete floor, which saves time and money on demolition costs.Cost-Effective: Epoxy coatings are a cost-effective flooring option. They are affordable compared to other flooring materials such as tile or hardwood. They also require minimal maintenance, which helps to reduce long-term costs.Environmentally Friendly: Epoxy coatings are a sustainable and environmentally friendly flooring option. They do not emit harmful fumes or pollutants, making them safe for both employees and the environment.In conclusion, industrial epoxy floor coatings are an excellent investment for any business that wants durable and attractive floors. They offer durability, easy maintenance, and improved safety, which makes them ideal for industrial environments. With a range of colors and patterns available, epoxy coatings also offer an opportunity to create a unique and customized floor that matches the branding and design of your business.
Extend the Lifespan of Your Water Tank with High-Quality Epoxy Coating in Central California
Water storage tanks are essential for homes, businesses, and industries to ensure a constant supply of clean and safe water. However, these tanks are also susceptible to corrosion, rust, and other damages due to exposure to water, chemicals, and other elements. To prevent such damages and ensure a longer lifespan for the tanks, epoxy coating for water tanks is an effective solution.What is Epoxy Coating For Water Tanks?Epoxy coating is a type of protective coating that is applied to metal surfaces to make them resistant to corrosion, rust, and other damages. This coating is made of a two-part mixture, which includes resin and hardener. When these two components are mixed, they react chemically to form a hard, durable coating that adheres tightly to the metal surface.Epoxy coating for water tanks is specifically designed to protect the metal from the harmful effects of water, chemicals, and other environmental factors. It acts as a barrier, preventing the metal from coming in contact with water and other substances that may cause damage or corrosion.Why use Epoxy Coating For Water Tanks?Water storage tanks are usually made of metals that are prone to rust and corrosion. Without proper protection, these tanks can deteriorate over time, which can lead to leaks, contamination, and other problems. Epoxy coating for water tanks provides a range of benefits that can help to prevent such issues:1. Long-lasting protection: Epoxy coating provides a durable and long-lasting protective layer that can withstand exposure to water and other elements. It can protect the metal from corrosion, rust, and other damages for several years.2. Cost-effective: Epoxy coating for water tanks is a cost-effective solution that can extend the lifespan of the tank. Instead of replacing the tank, which can be expensive, epoxy coating can be applied to restore the tank's functionality and prevent further damages.3. Reduced maintenance: Water tanks that are coated with epoxy require less maintenance than uncoated tanks. The coating prevents rust and other damages, which means fewer repairs and replacements are needed.4. Safe and clean water: Epoxy coating for water tanks is safe and non-toxic, which means it does not contaminate the water. It provides a clean and safe storage environment for the water.How is Epoxy Coating Applied to Water Tanks?The process of applying epoxy coating to water tanks is relatively simple. The tank surface is first cleaned and prepared for coating. This involves removing any dirt, rust, or other contaminants that may interfere with the bonding of the coating.Once the surface is clean, the epoxy coating is mixed according to the manufacturer's instructions. The coating is then applied to the tank surface using a spray gun, brush, or roller. The coating is left to cure for a specific amount of time, usually 24 to 48 hours, depending on the product used.After the coating has cured, it forms a hard, durable layer that provides long-lasting protection to the tank surface. The tank can then be filled with water and put into use.ConclusionEpoxy coating for water tanks is an effective solution for protecting metal surfaces from corrosion, rust, and other damages. It provides a durable and long-lasting protective layer that can extend the lifespan of the tanks and reduce maintenance requirements. When applied correctly, it provides a safe and clean storage environment for water. If you need water tank epoxy coating in Central California, Wright Tank has the expertise and experience to install high-quality coating to your metal water tank.
Leading Authority for Concrete Development and Education Programs Worldwide
, standards, technical resources, education, certification, expertise, design, construction, materials, and commitment.Concrete is an essential material used in the construction industry around the globe. It is a building block for roads, bridges, buildings, and other key infrastructure that supports urbanization and economic growth. However, the quality and safety of concrete structures rely heavily on the expertise and knowledge of those responsible for designing, constructing, and inspecting them.This is where the American Concrete Institute (ACI) comes in. As a leading authority and resource on all matters related to concrete, the ACI is dedicated to the development and distribution of consensus-based standards, technical resources, educational programs, certification programs, and proven expertise for individuals and organizations involved in concrete design, construction, and materials.The ACI has been at the forefront of advancing the knowledge and application of concrete since its inception in 1904. Over the years, it has developed numerous standards and guidelines that have become industry standards in the United States and around the world. These standards cover a wide range of topics, from the design and durability of concrete structures to testing and inspection techniques, making them indispensable to anyone working with concrete.One of the key strengths of the ACI is its technical resources, which are available in the form of books, journals, and electronic resources. These resources are written by leading experts in the field and cover a wide range of topics, from the basics of concrete design to the latest advances in materials science and technology. They provide valuable insights and practical advice that can help architects, engineers, contractors, and inspectors make informed decisions about the use of concrete in their projects.In addition to its technical resources, the ACI also offers a range of educational programs that are designed to enhance the knowledge and skills of professionals working in the concrete industry. These programs range from onsite training and seminars to online courses and certification programs. By participating in these programs, individuals can earn continuing education credits, enhance their professional credentials, and stay up-to-date with the latest industry developments.One of the core missions of the ACI is to promote a culture of commitment to the best use of concrete. This is reflected in the Institute's vision and values, which emphasize excellence, collaboration, integrity, and innovation. By fostering this culture of commitment, the ACI seeks to ensure that concrete structures are designed, constructed, and inspected to the highest standards of safety, durability, and sustainability.In conclusion, the American Concrete Institute is a vital resource for anyone involved in the design, construction, and inspection of concrete structures. Its standards, technical resources, educational programs, certification programs, and proven expertise are essential for ensuring the quality and safety of concrete structures around the world. If you are involved in the concrete industry, we encourage you to explore the ACI's offerings and become part of its community of professionals committed to the best use of concrete.
Epoxy Table Top with Wooden Herringbone Dining Design and Gloss Finish
: How to Create a Stunning Tabletop Epoxy FinishTabletop epoxy is becoming increasingly popular due to the stunning glossy finish it provides to wooden tables. It not only enhances the natural beauty of the wood but also protects from scratches, heat, and water damage. With the right tools and techniques, you can easily create a beautiful epoxy finish for your table.PreparationBefore starting, make sure your table is clean, dry, and sanded to perfection. Any imperfections in the wood surface will be highlighted by the epoxy, so it's important to make sure the surface is smooth and even.Mixing the EpoxyTo create the epoxy finish, you'll need a high-quality epoxy resin and hardener. Mix the two components according to the instructions provided by the manufacturer. It's crucial to follow the instructions carefully to ensure that the epoxy cures properly.ApplicationApply a thin layer of epoxy using a foam brush or roller. It's important to work quickly as the epoxy will start to set within 20-30 minutes. Spread the epoxy evenly across the table, making sure to cover all the edges and corners.Allow the first layer to cure for at least 24 hours. Once it has hardened, lightly sand the surface with fine-grit sandpaper to remove any bubbles, bumps, or rough spots. Then, apply a second layer of epoxy in the same manner as before.Finishing TouchesAfter the final layer of epoxy has been applied, let it cure for at least 48 hours. To achieve a perfect finish, lightly sand the surface once again with fine-grit sandpaper to remove any imperfections. Then, add a final layer of epoxy to create a deep, glossy finish.ConclusionCreating a tabletop epoxy finish is a simple and effective way to protect your wooden tables while also enhancing their natural beauty. By following the above steps and using high-quality materials, you can achieve stunning results that will last for years to come.Keywords: Tabletop Epoxy, epoxy resin, wooden tables, glossy finish, protect, scratches, heat, water damage, sanding, foam brush, hardener, instructions, curing, sandpaper, imperfections, deep, glossy finish.
Water-Based Resin Market Expected to Reach $10.5 Billion by 2020 with Increasing Demand in Various Industries
Water based resins are becoming increasingly popular in the market due to their eco-friendly nature, compatibility with various substrates, and superior performance properties. The global water based resin market is expected to reach $10.5 billion by 2020, and one type of water based resin that is gaining traction is water based acrylic resin powder.Water based acrylic resin powder is a type of polymer that is made by emulsion polymerization of acrylic monomers. It is a versatile material that can be used in a wide range of applications such as adhesives, coatings, inks, and others. It is also compatible with various substrates such as plastics, metals, and wood, making it an ideal choice for different end-user industries.One of the major advantages of water based acrylic resin powder is its ability to provide excellent adhesion properties. It can be used as an adhesive to bond different materials together, providing a strong and durable bond. Its adhesion properties make it ideal for applications such as laminating films on paper and bonding textiles.Another advantage of water based acrylic resin powder is its excellent film-forming properties. It can be used to form coatings on various substrates, providing a protective layer and enhancing the appearance of the substrates. Its film-forming properties make it ideal for applications such as coatings for metal and plastic substrates.In the ink industry, water based acrylic resin powder is used as a binder for pigments. Its excellent binding properties provide a strong and durable bond between the pigments and the substrate, resulting in high-quality prints. It is also easy to emulsify, making it ideal for use in water-based inks.With its eco-friendly nature and superior performance properties, water based acrylic resin powder is becoming increasingly popular in different end-user industries such as automotive, packaging, construction, and textiles. It can replace traditional solvent-based resins, which are harmful to the environment and human health.In conclusion, the water based resin market is growing, and water based acrylic resin powder is a type of water based resin that is gaining traction due to its excellent adhesion and film-forming properties. Its versatility makes it an ideal choice for different end-user industries such as automotive, packaging, construction, and textiles. Its eco-friendly nature and superior performance properties make it a great alternative to traditional solvent-based resins.
Uses of Epoxy Resin in Adhesive, Clear Coat, and Fiberglass Lamination
Epoxy Resin Coating For Wood - A Comprehensive GuideEpoxy resin is a popular choice for coating and protecting wood surfaces. It is a versatile material that can be used for a variety of purposes, including as an adhesive, clear coat, or for laminating fiberglass. In this blog post, we will discuss the benefits of using epoxy resin as a coating for wood and provide a guide for how to apply it properly.What is Epoxy Resin?Epoxy resin is a synthetic polymer that is made by mixing two components - a resin and a hardener. When these two components are mixed together, they undergo a chemical reaction that creates a material with excellent strength, durability, and chemical resistance. Epoxy resin is commonly used in industrial and commercial applications, but it also has many uses in the DIY world.Benefits of Using Epoxy Resin Coating for WoodThere are several benefits to using epoxy resin as a coating for wood, including:1. Protection from moisture and UV rays - Epoxy resin is excellent at protecting wood from moisture damage and UV rays. It forms a durable barrier that prevents water from penetrating the surface of the wood, which can lead to warping, cracking, and rotting. It also provides UV protection, which prevents the wood from fading and discoloring over time.2. Scratch and impact resistance - Epoxy resin has excellent scratch and impact resistance, which makes it ideal for high-traffic areas like floors and tabletops. It can withstand heavy use without showing signs of wear and tear.3. Chemical resistance - Epoxy resin is highly resistant to chemicals, including solvents, acids, and alkalis. This makes it an excellent choice for environments where chemicals are present, such as garages and workshops.4. Aesthetic appeal - Epoxy resin coatings can be customized to create unique designs and finishes. They can be tinted to any color, and additives like glitter, marble dust, and metallic pigments can be added to create a variety of effects.How to Apply Epoxy Resin Coating for WoodBefore applying an epoxy resin coating, it is essential to prepare the wood surface properly. Here are the steps to follow:1. Sand the wood surface - Sand the wood surface with a coarse-grit sandpaper to remove any rough spots, blemishes, or impurities. Then, sand it again with a fine-grit sandpaper to create a smooth surface.2. Clean the surface - Use a clean cloth or tack cloth to remove any dust or debris from the surface of the wood. Any particles left on the surface can cause imperfections in the epoxy resin coating.3. Apply a wood sealer - Apply a wood sealer to the surface of the wood. This will help to prevent any air bubbles from forming in the epoxy resin coating.4. Mix the epoxy resin - Follow the manufacturer's instructions to mix the epoxy resin and hardener together. Mix it thoroughly, making sure there are no lumps or bubbles in the mixture.5. Apply the epoxy resin coating - Pour the epoxy resin mixture onto the wood surface and spread it out evenly using a squeegee or roller. Make sure to cover the entire surface of the wood. Remove any air bubbles using a heat gun or blowtorch.6. Allow to dry - Allow the epoxy resin coating to dry for at least 24 hours before using the surface.ConclusionEpoxy resin coatings are a popular choice for protecting and enhancing the appearance of wood surfaces. They offer excellent durability, chemical resistance, and can be customized to create a variety of effects. By following the steps outlined in this guide, you can apply an epoxy resin coating to your wood surface properly and enjoy all the benefits it has to offer.
Leading Manufacturer Showcases Innovative Solutions for Industrial Applications
In recent years, the furniture industry has experienced a rise in demand for polyurethane (PU) foam. This is due to the unique properties of PU foam, including its softness, flexibility, and durability. However, the production of PU foam can be challenging, especially when it comes to the trimming process. That is where Tri-Mer Corp. comes into play.Tri-Mer Corp. is a leading manufacturer of air pollution control systems, industrial process equipment, and fluid handling systems. The company has been providing innovative solutions to a variety of industries, including furniture, automotive, and aerospace, for over 50 years. However, Tri-Mer Corp. has recently gained recognition for its innovative PU trimer system, which is designed to make the production of PU foam more efficient and environmentally friendly.The PU trimer system developed by Tri-Mer Corp. is a unique technology that offers significant benefits to companies that produce PU foam. The system is designed to minimize waste and reduce the amount of harmful emissions released into the environment during the production process. This is achieved by utilizing a patented process that involves the simultaneous conditioning of the air and the foam. This results in a significant reduction in energy consumption and the ability to meet strict environmental regulations.One of the most impressive features of the Tri-Mer Corp. PU trimer system is its ability to produce high-quality PU foam products consistently. This is particularly important in the furniture industry, where the quality of furniture depends on the quality of the foam used. With the PU trimer system, Tri-Mer Corp. can produce foam that meets the highest standards, ensuring that furniture manufacturers can provide their customers with products that are comfortable, durable, and long-lasting.Another benefit of the PU trimer system is its ease of use. The system is designed to be user-friendly, providing operators with a straightforward process that requires minimal maintenance. This means that furniture manufacturers can integrate the system into their production line easily, without the need for significant capital investments.Tri-Mer Corp. is committed to providing innovative solutions to the furniture industry and other industries that rely on PU foam. With its PU trimer system, the company is helping to reduce waste, decrease energy consumption, and meet strict environmental regulations. Moreover, the system allows for the production of high-quality foam products that are comfortable and durable. By continuing to invest in research and development, Tri-Mer Corp. is poised to remain a leader in air pollution control systems, industrial process equipment, and fluid handling systems for many years to come.In conclusion, the Tri-Mer Corp. PU trimer system is a game-changer for the furniture industry and other industries that rely on PU foam. The system offers numerous benefits, including reduced waste, decreased energy consumption, and the ability to meet strict environmental regulations. Moreover, the system produces high-quality foam products that are comfortable and durable. By investing in the PU trimer system, companies can significantly improve their production process, reduce costs, and enhance their environmental profile.
Hydroxy Acrylic Resin for Industrial Coatings - High Solid Content, Excellent Adhesion, and Chemical Resistance
Hydroxy Acrylic Resin for Industrial Coating: Sanben's Solution for High-Performance CoatingsSanben is a leading producer of hydroxy acrylic resin for industrial coating, offering an innovative solution for the production of high-performance coatings. The company's RA6066 resin is a versatile and cost-effective material that provides outstanding properties, including excellent hardness, adhesion, and chemical resistance.Sanben's RA6066 is a waterborne hydroxy acrylic resin that can be formulated into a wide range of coatings, such as wood coatings, metal coatings, and plastic coatings. The resin's high solid content, low VOC emissions, and excellent coating properties make it an ideal choice for industrial coating applications requiring superior performance and environmental compliance.One of the key features of RA6066 is its outstanding adhesion to various substrates, including metals, plastics, and wood. The resin provides excellent wetting properties, leading to a strong bond between the coating and the substrate. This allows for the production of high-performance coatings with excellent corrosion resistance, weatherability, and durability.Another vital property of the RA6066 resin is its hardness. Sanben's hydroxy acrylic resin offers excellent scratch resistance and abrasion resistance, making it an ideal material for demanding industrial applications. By incorporating RA6066 into a coating formulation, manufacturers can produce coatings that can withstand harsh environments and provide long-lasting protection to their products.Moreover, RA6066 has excellent chemical resistance and can withstand exposure to a wide range of chemicals, including acids, alkalis, and solvents. This property is crucial for coatings used in industries involving harsh chemicals and frequent cleaning, such as the automotive, aerospace, and food and beverage industries.Sanben's hydroxy acrylic resin also provides excellent film-forming properties. The resin creates a smooth, uniform coating film with a high gloss finish, improving the appearance of the coated product. Additionally, the resin's low VOC emissions and waterborne nature make it an environmentally friendly solution for industrial coating applications.In conclusion, Sanben's RA6066 hydroxy acrylic resin is an innovative solution for the production of high-performance industrial coatings. Its outstanding adhesion, hardness, chemical resistance, and film-forming properties make it an ideal material for a wide range of coating applications, from wood and metal to plastics and composites. Sanben's commitment to providing high-quality, environmentally friendly industrial materials makes them a trusted provider in the field of industrial coatings.